Advisor
Jane Li (zli11@wpi.edu)
Assistant Professor with Robotics Engineering and Mechanical Engineering
Jie Fu (zli11@wpi.edu)
Assistant Professor with Robotics Engineering and Electrical & Computer Engineering
Academic Year: 2017-2018
Major: RBE, ME, ECE
Project Members:
- Nguyen, Duong (dnguyen2@wpi.edu)
- Nguyen, Hoang P. (hpnguyen@wpi.edu)
- Dinh, Thai Si (tsdinh@wpi.edu)
Project Goal
- Design and manufacture a robotics hand for Baxter from the TRINA system based on the Reflex SF from RightHand Robotics, Inc.
- Create a glove to gather motion data from the user and directly control the robotics hand.
- Both the hand and the glove will be fully functional and compatible with ROS to run with the already existed TRINA system.
Approach
- Hardware design
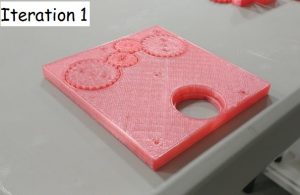
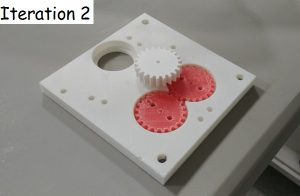
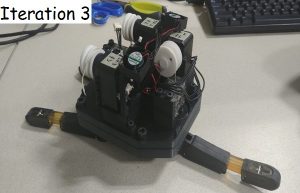
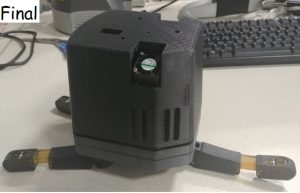
- Software design
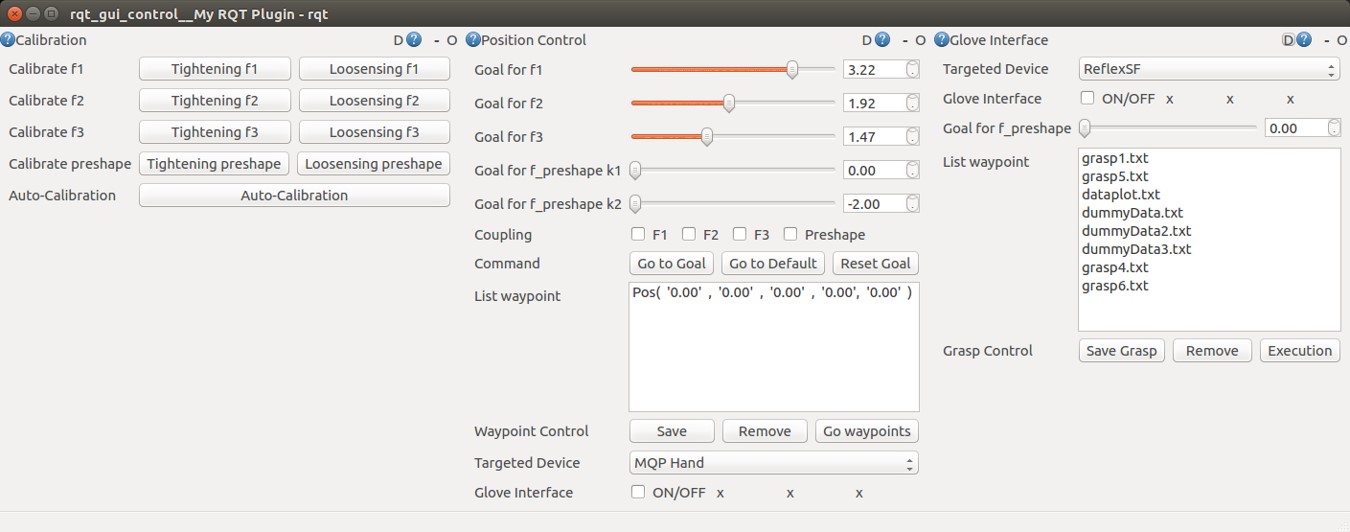
- Glove integration
The motivation for using a glove to directly control the robotics hand comes from the VR gloves, which ultimately allows the user to use hand motions directly to provide inputs. However, after sourcing from multiple companies, most of the gloves are Windows compatible only. This problem can be solved by creating a virtual host to allow communication between Windows and the ROS node on Linux. Since there are multiple layers of data transmission, the packets got dropped frequently and are very slow. Therefore, the team decided to keep the textile of the glove while implementing different electrical components that are ROS compatible. Ultimately, the control glove consists of a textile from CaptoGlove company, three flex sensors directly connected to an Arduino Nano that will be sending data to the ROS node.
Result and Demonstration videos
With the hardware built and controller glove integrated, the robotic manipulator system has been able to perform various tasks. Firstly, the hand was able to pick up various objects with different shapes without having to go through extensive grasp planning, even with deformable objects. Secondly, with the aid of the control glove, the robotis hand has been able to successfully manipulate a board eraser and a cup.